Plastic extrusion for economical product fabrication
Plastic extrusion for economical product fabrication
Blog Article
Key Advantages and Considerations of Executing Plastic Extrusion in Your Projects
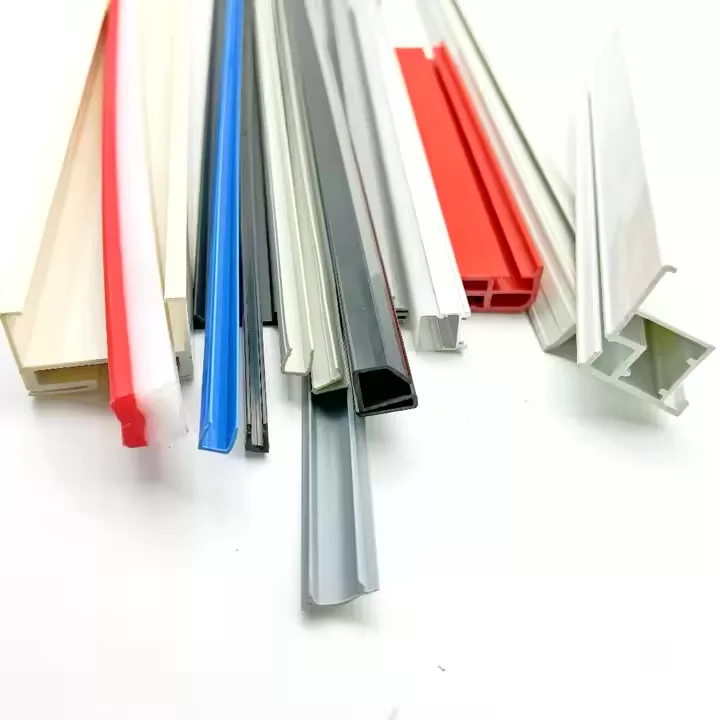
Comprehending the Fundamentals of Plastic Extrusion
Plastic extrusion, a staple in the production sector, is a procedure that includes melting raw plastic material and reshaping it into a continuous profile. This account, as soon as cooled down, can be cut into wanted sizes or coiled for later use. The beauty of plastic extrusion lies in its versatility. A wide array of items, from piping to window frames, can be generated. The process requires an extruder, an intricate equipment with a warmed barrel, a rotating screw, and a die at the end. The plastic material, in the kind of pellets, is fed into the extruder, where it's melted and compelled with the die, taking its shape. The selection of plastic and the style of the die figure out the product's features.

The Economic Benefit of Plastic Extrusion
The economic advantage of plastic extrusion exists primarily in 2 areas: cost-effective product manufacturing and beneficial manufacturing speeds. With plastic extrusion, organizations can create high volumes of product at a lower price contrasted to other methods. The process flaunts a remarkable production speed, considerably lowering time and more enhancing its economic feasibility.
Cost-efficient Material Production
A considerable advantage of plastic extrusion is its impressive cost-effectiveness. Additionally, the extrusion process allows for a high level of precision in forming the plastic, decreasing the demand for expensive post-production alterations or improvements. All these elements make plastic extrusion a very cost-effective choice for lots of projects, supplying an appealing balance in between expense and efficiency.
Beneficial Production Speeds
While maintaining the cost-effectiveness of the products, one more noteworthy benefit of plastic extrusion depends on its rapid manufacturing rates. This performance in the production process is attributed to the continual nature of the extrusion process, permitting high-volume manufacturing in a relatively brief time period. The speed of production straight correlates to a reduction in labor costs and a rise in output, thereby enhancing the general financial feasibility of the procedure. Moreover, the hectic production does not compromise the high quality of the end product, guaranteeing regular and trustworthy results. This combination of rate, cost-effectiveness, and high quality emphasizes the substantial financial benefit of implementing plastic extrusion in various projects.
Versatility and Personalization: The Staminas of Plastic Extrusion
Among the noticeable strengths of plastic extrusion lies in its versatility and customization capacity. These high qualities unlock to endless design possibilities, providing suppliers the ability to tailor products to particular demands. This increased level of customization not just improves product capability however also considerably boosts item uniqueness.
Limitless Style Possibilities
Plastic extrusion radiates in its capability to use practically endless layout opportunities. This method supplies liberty to create detailed profiles and complicated forms, an accomplishment hard to attain with other manufacture methods. Owing to the fluid nature of liquified plastic, the process is versatile enough to generate a varied array of types, dimensions, and sizes. The plastic can be adjusted to match special specifications, enabling the manufacturing of personalized geometries and meeting click here now specific customer demands. Plastic extrusion can manage a selection of plastic kinds, broadening its application range. This versatile technique, consequently, offers a variety of sectors from building to automobile, product packaging to electronics, and beyond. With plastic extrusion, the style opportunities are essentially endless.
Increasing Product Uniqueness
The adaptability of plastic extrusion can substantially boost product originality. This procedure permits developers to explore various shapes, sizes, and colors, giving them the flexibility to produce distinct products that stand apart out there. It is this personalization that provides an unique identification to every product, differentiating it from its competitors.
In addition to its aesthetic advantages, the customizability of plastic extrusion also supplies sensible advantages. Designers can customize the homes of the plastic according to the particular requirements of the application, boosting the item's functionality. For circumstances, they can make the plastic much more adaptable, more sturdy, or a lot more resistant to warmth, depending upon what the product calls for. Hence, plastic extrusion not only enhances product originality yet additionally its energy and bankability.
Design Limitations in Plastic Extrusion: What You Need to Know
Just how can create constraints potentially influence the procedure of plastic extrusion? While plastic extrusion is functional, layout limitations can reduce its advantages. Recognizing these restraints is crucial for effective execution of plastic extrusion in your tasks.
Evaluating the Ecological Impact of Plastic Extrusion
While understanding design limitations is a considerable element of plastic extrusion, it is similarly essential to consider its environmental ramifications. The process of plastic extrusion includes melting plastic materials, potentially releasing dangerous gases right into the atmosphere. Further, the resulting products are frequently non-biodegradable, adding to land fill waste. Improvements in innovation have enabled for more environmentally-friendly practices. As an example, utilizing recycled plastic materials in the extrusion process can decrease environmental impact. Additionally, establishing naturally degradable plastic choices can aid reduce waste issues. Examining these environmental variables is vital when executing plastic extrusion projects, making sure a balance in between effectiveness, cost-effectiveness, and ecological duty.
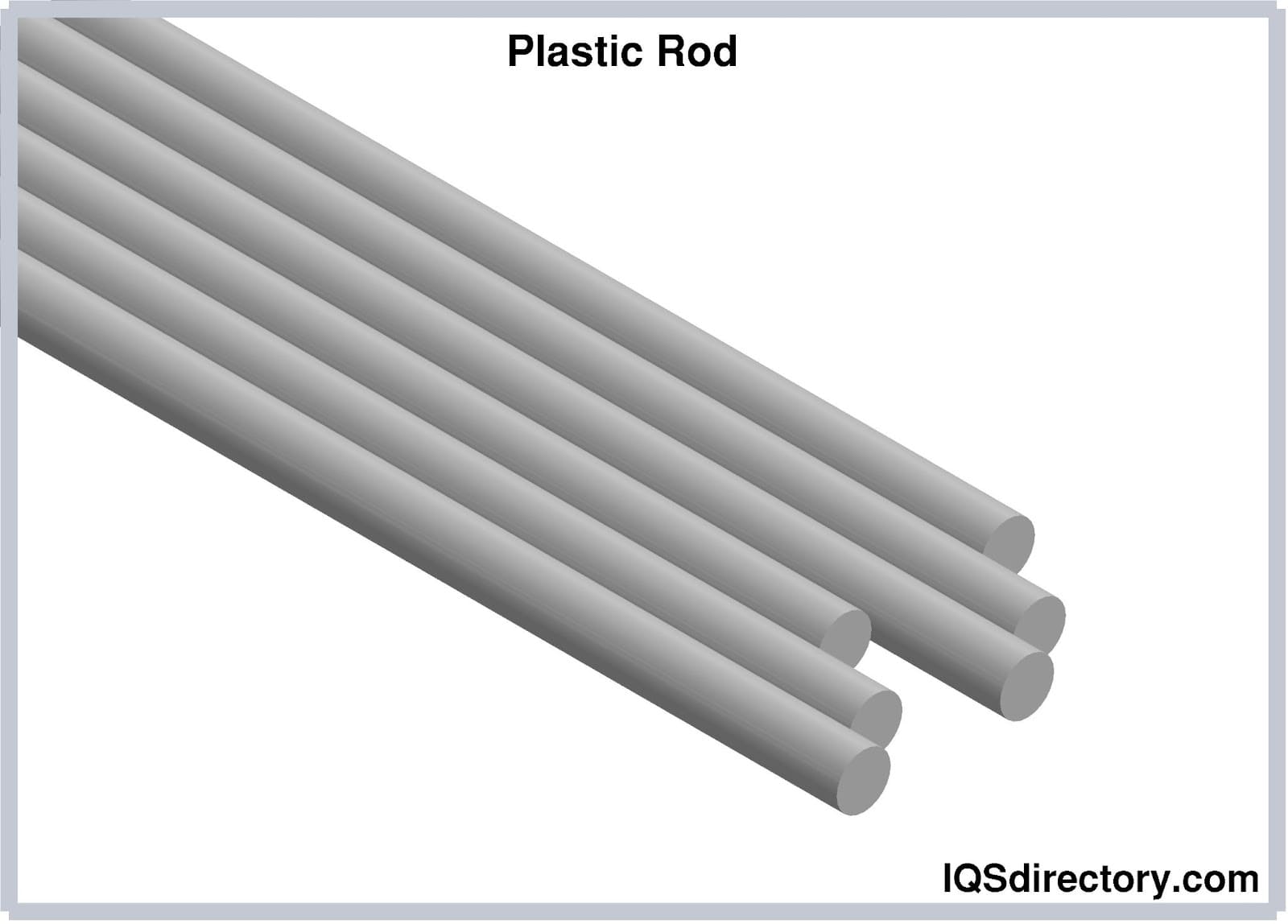
Study: Successful Projects Using Plastic Extrusion
Success tales in the area of plastic read extrusion are plentiful, showing both the flexibility and performance of this manufacturing process. plastic extrusion. Another successful instance is the production of plastic film other for packaging and agriculture. These circumstances highlight plastic extrusion's crucial role in different industries, testifying to its versatility, cost-effectiveness, and trusted output.
Conclusion
In final thought, plastic extrusion uses a effective and economical method for generating complicated forms with very little waste. While it supplies countless benefits such as cost-effectiveness and convenience, it's critical to take into consideration potential layout limitations and environmental impacts. Implementing recycled or eco-friendly products can mitigate these problems, boosting sustainability. Incorporating plastic extrusion right into projects can result in effective outcomes, as confirmed by countless case studies.
Plastic extrusion, a staple in the manufacturing market, is a procedure that entails melting raw plastic product and improving it into a continuous profile. Plastic extrusion can manage a selection of plastic kinds, expanding its application range.Just how can make limitations possibly influence the process of plastic extrusion? The procedure of plastic extrusion involves melting plastic products, potentially releasing hazardous gases into the atmosphere. Making use of recycled plastic products in the extrusion procedure can reduce environmental impact.
Report this page